Polyblend®, Dynablend™ and Miniblend™
Polyblend® and Dynablend™ - The De-Facto Standard for Professionals
For decades, Polyblend® has been the name synonymous with the optimization of water and wastewater polymer usage. The two‐zone Polyblend® and Dynablend™ mixing regimen is widely recognized by polymer experts and manufacturers as the proper mixing methodology to optimize polymer activation. The high shear mixing zone followed by lower energy dissolution and finally a final post‐dilution step has been proven as the best mixing methodology for today’s higher molecular weight polymers.
With thousands of installations around the world, Polyblend® and Dynablend™ polymer activation systems not only represent the best science of polymer blending, but are the de‐facto standard for serious water and wastewater professionals interested the best polymer efficiencies.
Polyblend's Long History of Excellence
The Polyblend® technology was introduced in 1972. UGSI Chemical Feed, Inc. pioneered the development of cost-effective polymer activation technologies for use in water and wastewater applications by simply following the science of polymer activation.
Polyblend® and Dynablend™ systems consistently achieve higher viscosities and activation levels than other polymer mixing systems and are designed for both emulsion polymer and dry polymer applications.
cleanwater1 is proud to offer the most comprehensive line of both mechanical and hydraulic polymer activation feeders.
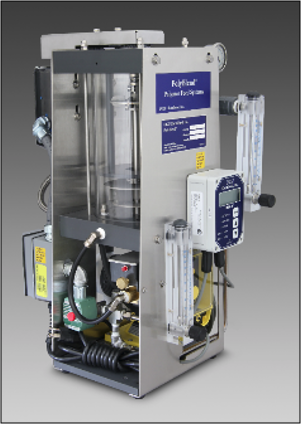
Polyblend® systems consistently achieve higher viscosities and activation levels than other polymer mixing systems.
The Science of Efficient Polymer Activation

High Energy at MOIW
+
Transition to Low-Energy "Quiescent Zone"
+
=
Fully Activated Polymer Solution at Desired Concentration
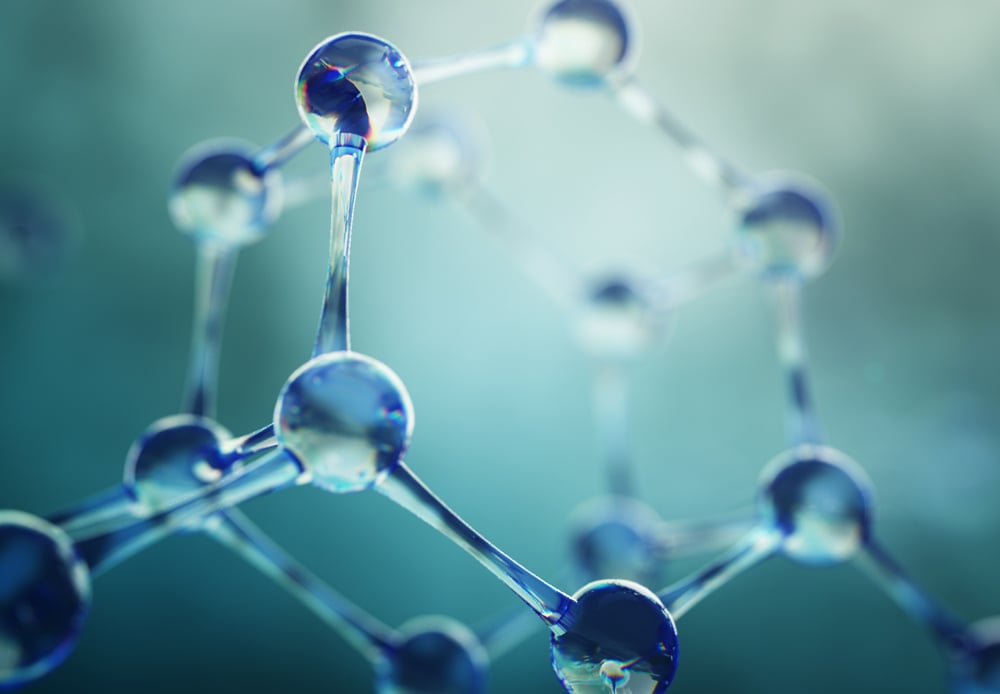
We Follow the Science
Our systems are designed to optimize polymer performance because they follow the latest in polymer science. These fundamental aspects are demonstrated in our feeders:
- Two stage mixing with the highest energy applied first at the moment of initial wetting (MOIW) followed by a "quiescent" zone allowing for more gentle activation as polymer science dictates.
- Extended residence time in the "quiescent" zone to optimize the continued charge site exposure as the polymer is activated in an optimal manner.
How We Achieve High Activation Levels and High Viscosities
Polymers vastly improve the operations of water and wastewater plants by accelerating settling of particles and improving sludge dewatering. To get optimal “uncoiling” of polymer chains without damaging or shortening the polymer chain, different levels of energy must be applied to the polymers at different times. High energy mixing is required to prevent agglomerations, but over-mixing can damage the polymer. The key is to shift mixing energy over time to get the optimal results.
Our Polyblend® and Dynablend™ Liquid polymer feed systems apply high energy at the moment of initial wetting (MOIW) followed by a transition to a low-energy quiescent zone. This enables our Polyblend® and Dynablend™ polymer mixing systems to consistently achieve higher activation levels and viscosities.
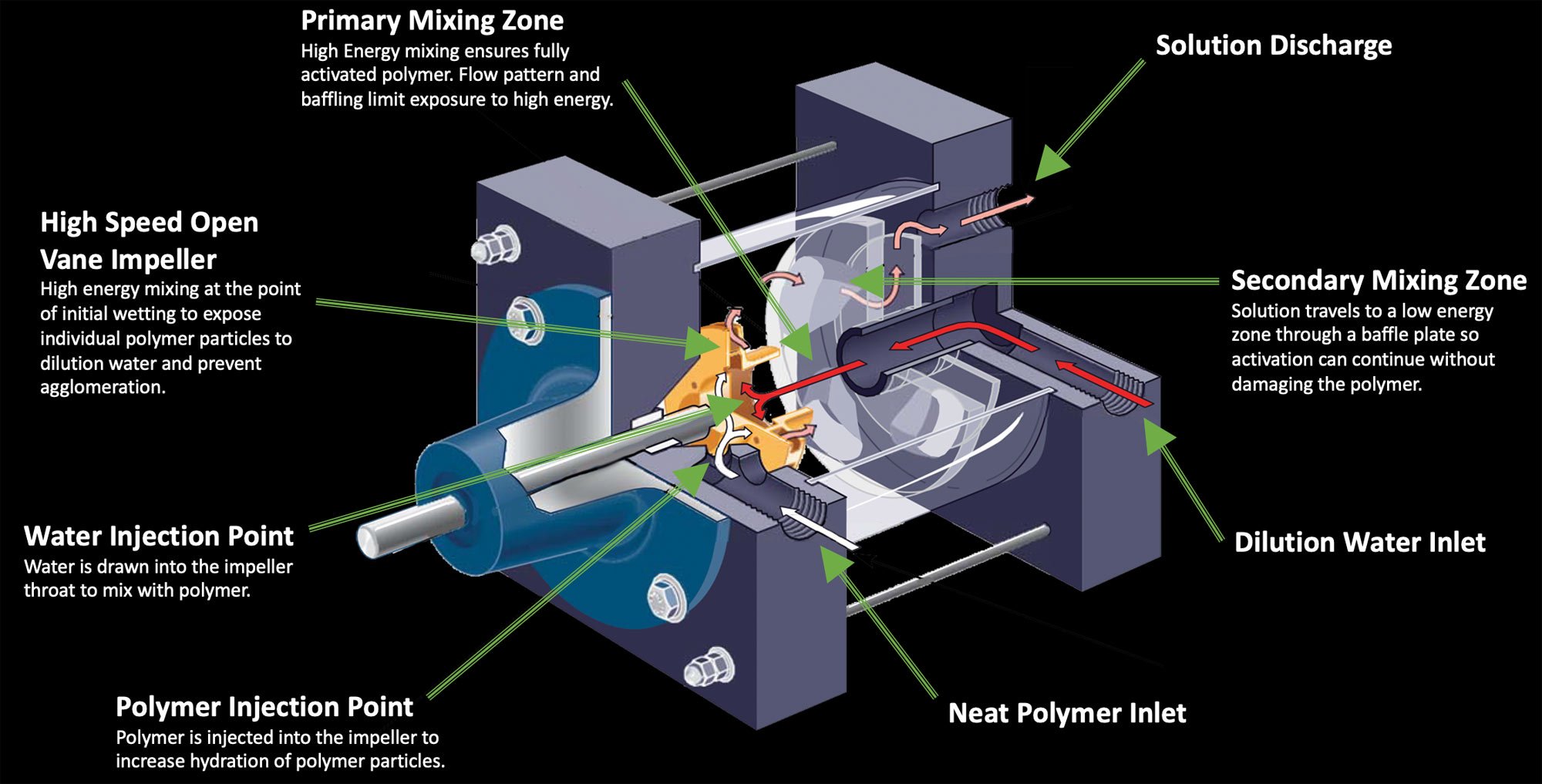
Our Emulsion Polymer Activation Technology
cleanwater1's industry-leading emulsion polymer activation technologies use superior two-stage mixing to achieve superior results. We frequently see higher polymer savings with two-stage mixing compared to single-stage mixing. Optimizing mixing energy ensures consistent performance. This allows us to handle new polymer developments, ultra-high molecular weights, different charge densities and new chemistries. The compact size and open-frame design enables easy installation, access, and maintenance in confined spaces. Control options range from simple manual to full PLC-based automatic control with complete SCADA interface.
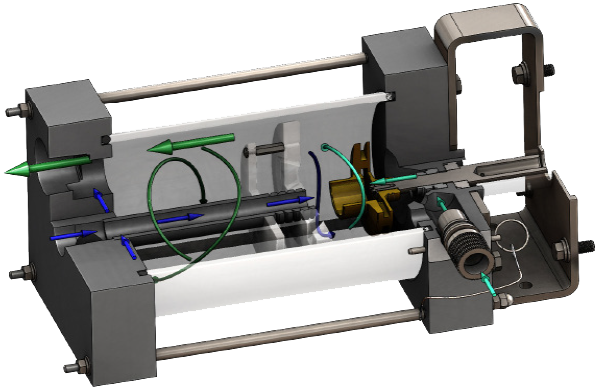
Benefits of Polyblend® Mechanical Mixing
- Highly efficient mixing process results in polymer savings
- Excels at high molecular weight polymers
- Ability to quantify the energy input and relate it to G value (important for high molecular weight polymers or polymers with a tight tolerance for activation)
- Low maintenance cost
- Wide variety of size options
- Large installation base
Benefits of Dynablend™ Hydraulic Mixing
- Performs well with wide range of molecular weight polymers
- No moving parts in the mixing chamber
- Low operating cost
- Low maintenance cost
- Multiple mixing chamber sizes
- Highly reliable
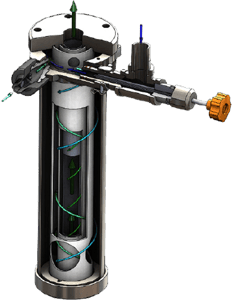
Polyblend® PB Series
At the center of the PolyBlend® PB Series polymer feed system is the unique multi-zone mixing chamber. The advanced design provides uniform dispersion energy at the moment of initial wetting. The high-energy mix prevents agglomerations and eliminates the need for extended mixing and aging by applying the right energy at the right time. The low-energy zone continues to activate the hydrated polymer without destroying the fragile polymer chains.
The result is maximum polymer activation and improved polymer performance. The compact design of the PolyBlend® PB Series provides easy installation. The corrosion-resistant, stainless steel chassis houses the lightweight system allowing for easy mobility.
The PB is ideal for portable use or where intermittent use requires the system to be stored in one location and used in another. Various models cover a polymer solution flow range from 0.1 to 20 USGPM.
Unlike most polymer feeders, the PB series works equally well at very low flow rates.

Features
- Maximum polymer activation
- Innovative multi-zone mixing chamber
- Simplified electronic controls
- Light, compact, portable design for easy mobility
- Corrosion-resistant
- Available in large and small frames
Benefits
- More for less
- The right energy at the right time
- Great for areas requiring small footprint
- Works well at very low flow rates
- Eliminating agglomerations reduces polymer use
- Trusted and proven technology
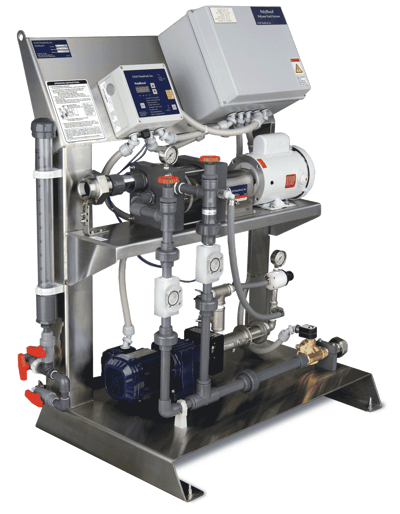
Polyblend® M Series, Magnum and M-Lo Liquid Polymer Series
The PolyBlend® M Series is engineered for quick, easy installation and service and is built to last. The compact size of the feeder allows trouble-free installation in confined spaces, and the open-frame design facilitates easy component access. The M Series is engineered to handle the harshest environments and is designed to handle new polymer developments, ultra-high molecular weights, different charge densities, and even totally new chemistries.
The PolyBlend® Magnum achieves even higher viscosity solutions than the M Series by enhancing the proven two-zone mixing energy profile with the 14,000 sec-1 G-Value. The carefully sized volume of the Magnum low energy mix zone increases polymer residence time and accelerates the “hydration/relaxation” of the activated polymer chains resulting in increased viscosity and ultimate performance.
The Polyblend® M-Lo Series liquid polymer feed system provides consistent and accurate dosage to improve polymer efficiency. It offers all of the benefits of the best available polymer preparation system at a competitive price. The ready-to-install system provides consistent and accurate dosage and improves polymer efficiency. Seven models are available with outputs of 0.4 to 2.5 GP.
Features
- Improved polymer efficiency
- Rugged & reliable design
- Direct drive mix chamber
- Simple electronic controls
- Competitive price in large and small frames
Benefits
- Provides consistent and accurate dosage
- Open-frame design offers easy access to components
- Compact size works well in confined spaces
- Easy installation & maintenance
- Several models are available to cover a wide range of dosage rates
Dynablend™
Dynablend™ liquid polymer blending systems are proven to be the most effective and reliable hydraulic polymer activation technology.
The L4 and L6 are the smallest Dynablend™ units and the use of a peristaltic pump makes them the most economical of the Dynablend™ blending system. They use a patented Hydroaction technology. Dynablend offers a choice of peristaltic or progressive cavity pumps, depending on the application.
The L8 and L12 Dynablend™ liquid polymer blending systems include all features available throughout the line, but in larger capacities. The units are designed to provide the highest standard water and polymer flow rates on the market.
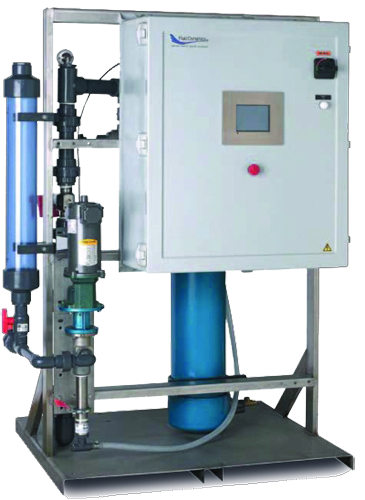
Features
- Patented hydroaction technology
- Two-stage mixing
- Highest energy applied at first at the moment of initial wetting (MIOW)
- Gentle activation in quiescent zone
Benefits
- Performs well with wide range of molecular weight polymers
- No moving parts in the mixing chamber
- Low operating cost
- Low maintenance cost
- Multiple mixing chamber sizes
- Highly reliable
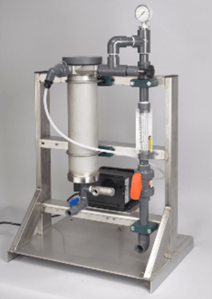
Miniblend™
Miniblend™ liquid polymer blending systems are proven to be the most effective and reliable polymer activation technology. Miniblend™ has easy-to-use controls and utilizes hydroaction concentric mixing chambers to activate simple-to-blend and difficult-to-blend polymers.
Miniblend™ is lightweight and portable and is available as a skid mounted or remote-mounted neat polymer metering pump.
Features
- Manual or automatic pump speed control
- Choice of diaphragm, peristaltic or remote-mounted neat polymer metering pump
- 304 stainless-steel frame and mixing chamber
Benefits
- Lightweight and portable
- Reliable, mixing chamber
- Lowest operating cost
- Most effective and reliable polymer feeders in the industry
"The PolyBlend® polymer activation systems have performed flawlessly since installation and will result in very significant polymer saving for our facility."
Polyblend Mechanical Activation (Emulsion Polymer)
Overview of Polyblend Mechanical Activation Series
Polyblend® PB Series
This original Polyblend® PB Series unit offers more for less by providing a compact design and maximum polymer activation with an innovative multi-zone mix chamber that provides uniform dispersion energy at the moment of initial wetting.
The PB is lighter than most other polymer feeders, making it ideal for portable use or where intermittent use requires the system to be stored in one location and used in another.
Various models cover a polymer solution flow range from 0.1 to 20 USGPM. Unlike most polymer feeders, the PB series works equally well at very low flow rates.
Available in a wide range of capacities up to 75 US gpm (280 l/min).
Small Frame
Features
- Trusted & Proven Technology- Maximum Polymer Activation
- Innovative Mixing Chamber
- Simplified Electronic Controls
- Compact Design
Benefits
- More for less- The right energy at the right time
- Great for areas requiring small footprint
- Works well at very low flow rates
- Polymer use is reduced by eliminating agglomerations
Large Frame
Polyblend® M Series
The PolyBlend® M Series combines proven motorized mixing technology with precise controls, a variety of pump offerings and an easy-to-service open-frame design. Then we add two unique options: variable speed mixing and automatic dosage control with constant solution strength.
The ready-to-install system provides consistent and accurate dosage and improves polymer efficiency. Seven models are available with outputs of 0.4 to 2.5 GP.
Available in a wide range of capacities up to 200 US gpm (760 l/min).
Features
- Improved Polymer Efficiency
- Open-Frame Design
- Direct Drive Mixing
- Optional Advanced Controls
- Pump Interchangeability
- Integral Post Dilution
Benefits
- Open Frame Design allows for all components to be easily accessed.
- Integral post dilution increases operational flexibility in fine-tuning system performance.
- Rugged base is suitable for wall, stand or floor mounting.
- Three choices of control packages are available to meet a wide variety of applications.
- Clear mixing chamber provides visual indication of polymer feed and mixer performance.
Polyblend® Magnum
The PolyBlend® Magnum achieves even higher viscosity solutions than the M Series by enhancing the proven two-zone mixing energy profile with the 14,000 sec-1 G-Value.
The carefully sized volume of the Magnum low energy mix zone increases polymer residence time and accelerates the “hydration/relaxation” of the activated polymer chains resulting in increased viscosity and ultimate performance.
Features
- High Energy/Low Energy Mixing Profile
- Ratio of low-to-high energy mix zone volume was increased to increase residence time (Ꚍ)
- High-energy mixing at the moment-of-initial-wetting (MOIW) to achieve maximum hydration (high viscosity) of the polymer particle in the shortest time
- Direct coupled 3,450 RPM motor eliminates the need for shaft alignment
- Quick Disconnect on the neat polymer injection check-valve (now available on all models as a separate kit - Eliminates the need for tools to access the check-valve for periodic cleaning
Polyblend® M-Lo Series
Engineered for easy installation and maintenance and ready-to-install, the system provides consistent and accurate dosage and improves polymer efficiency. Its compact size and trouble-free installation are ideal for confined spaces and the open-frame design facilitates easy component access.
Available in capacities from 0.4 to 2.5 US gph (1.5 to 9.5 lph).
Features
- Improved polymer efficiency
- Easy installation & maintenance
- Rugged & reliable design
- Direct drive mix chamber
- Simple electronic controls
- Competitive price
Benefits
- Provides consistent and accurate dosage
- Open-frame design offers easy access to components
- Compact size works well in confined spaces
- Several models are available to cover a wide range of dosage rates
Polyblend® M Series Control Options
Accessories
A multitude of accessories are available for your Polyblend® systems, including dry polymer extension hoppers and bulk bag frameworks, tables, drum mixers, air dryers, and more.
Overview of Dynablend™ Hydraulic Activation Series
Miniblend™
Lightweight and portable, Miniblend™ liquid polymer blending systems are proven to be the most effective and reliable polymer activation technology. Hydroaction technology follows the science of polymer activation. Two-stage mixing with the highest energy applied first at the moment of initial wetting (MIOW) followed by a "quiescent" zone allowing for more gentle activation as polymer science dictates.
Options:
- Choice of skid mounted or remote-mounted neat polymer metering pump.
- Explosion-proof Class 1 Div. 1 systems
Water Supply Pressure: Water supply must be able to provide the maximum flow rate at 2.4 bar (35 psig) greater than the pressure at feeder discharge
Maximum Operating Pressure: • 6.9 bar (100 psig)
Dimensions: • 475 mm x 610 mm x 1016 mm (18 in x 24 in x 40 in)
Weight: • 45 kg (100 lbs)
Power Equipment: • 120 VAC, 0.6 kW (5 Amp)
Dynablend™ Liquid L4 and L6 Polymer Systems
The L4 and L6 are the smallest Dynablend™ units and the use of a peristaltic pump makes them the most economical of the Dynablend™ blending system.
Patented Hydroaction technology follows the science of polymer activation.
Two-stage mixing with the highest energy applied first at the moment of initial wetting (MIOW) followed by a "quiescent" zone allowing for more gentle activation as polymer science dictates.
Choice of peristaltic or progressive cavity pumps, depending on application.
Dynablend™ Liquid L8 and L12 Polymer Systems
The L8 and L12 Dynablend™ liquid polymer blending systems include all features available throughout the line but in larger capacities.
The units are designed to provide the highest standard water and polymer flow rates on the market.
Patented Hydroaction technology follows the science of polymer activation. Two-stage mixing with the highest energy applied first at the moment of initial wetting (MIOW) followed by a "quiescent" zone allowing for more gentle activation as polymer science dictates.
Accessories
Numerous pump, control and instrument options are available.
Which Technology is Right for You?
Our team of trained experts can help determine the best technology for your application. Because we are not limited to one technology, you can feel confident knowing we’re committed to finding the system that meets your process objectives.
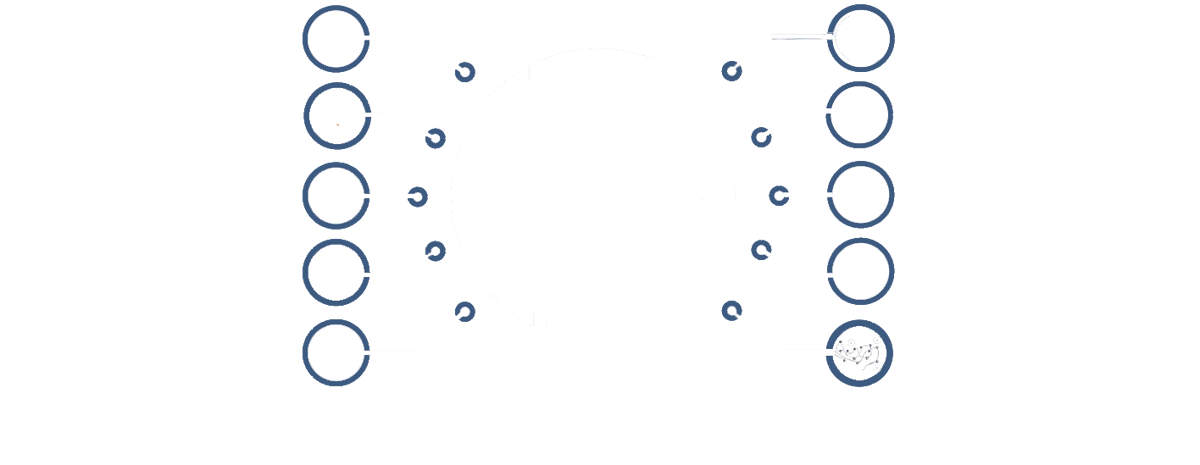
Featured Installations
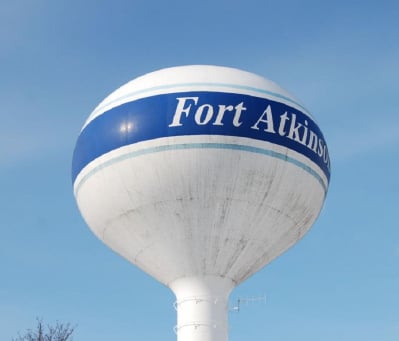
Fort Atkinson
Goal: Optimize their polymer system and lower Polymer costs.
Outcome: Overall polymer usage was decreased by 25-30% and efficiency was increased. The Polyblend® Magnum system decreased the average quantity of daily emulsion polymer usage from 35 gallons to 25 gallons. The introduction of the Polyblend® Magnum system allowed the City to save nearly $20,000 annually or 30% on costs. These savings were much higher than originally projected prior to testing and installation.
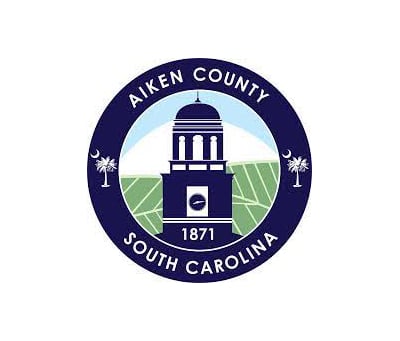
Aiken County
Goal: Find a more efficient, better quality alternative to the dry polymer dosing option they were using.
Outcome: Overall polymer usage went down almost immediately after the Polyblend® liquid polymer system was activated. Costs decreased by nearly 50% and quality of biosolids increased. With the demonstrated improvement in sludge quality and the roughly 50% savings in polymer, the plant decided to purchase a Polyblend® Magnum unit for one BFP line and prepared to purchase another for the other BFP line later in the calendar year.
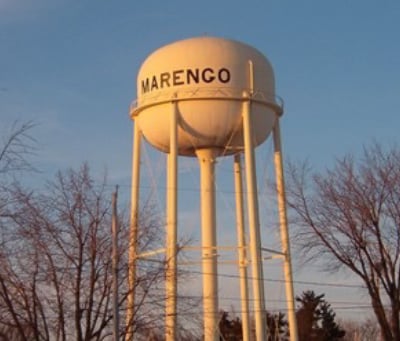
City of Marengo
Goal: Replace their old sludge processing system with one that could produce sludge that could be used as fertilizer.
"PolyBlend® has been performing exceptionally well for Windsor, Ontario, for over two decades. With basic maintenance, we’ve needed very few parts over the years, and when you see the equipment, it is in excellent condition!"
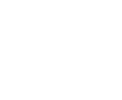
Let's get the conversation started
Tell us a little bit about you and the information you’re looking for and we'll send you information by email about the topics you are interested in. Check the box to have a cleanwater1 expert contact you within one business day.
Additional Resources
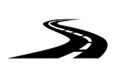
Learn At Your Pace
By subscribing to our learning track, you will receive emails featuring videos, webinar invites, informative articles and more.

View Our Online Library
Featuring brochures, case studies, data sheets and more. Filter by product category, brand, location, use case or document type.

Connect With Us
Contact a member of our team using our online form, by email or give us a call. We look forward to speaking with you.