Polyblend® and Dynajet™
Our Dry Polymer Systems
The Unmatched Reputation of Polyblend® and Dynajet™
Polyblend® DP systems have an unmatched reputation for reliability. The DP system typically reduces polymer consumption by 25% or more, while substantially improving polymer performance in terms of sludge dryness, solids capture, water clarity, drainage / retention, or any other measure. In head-to-head trials, the Polyblend® DP110 Dry Polymer Feed System outperforms all other designs. While dry polymer feed systems are notoriously high maintenance items, the Polyblend® DP Series requires the least maintenance and operates unattended for a longer interval than any other dry polymer feed system on the market.
The Dynajet™ technology uses a blower-induced pneumatic conveyance system to transfer up to 12 lbs of polymer per minute from the volumetric feeder to the wetting head. The polymer is naturally dispersed in the conveyance air before introduction to the dilution water for optimum polymer-particle wetting.
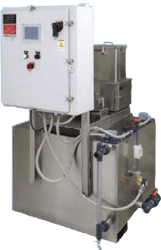
The DP110 Dry Polymer System, shown above, outperforms all other designs in head-to-head trials.
The Science of Efficient Polymer Activation

High Energy at MOIW
+
Transition to Low-Energy "Quiescent Zone"
+
=
Fully Activated Polymer Solution at Desired Concentration
We Follow the Science
Our systems are designed to optimize polymer performance because they follow the latest in polymer science. These fundamental aspects are demonstrated in our feeders:
- Two stage mixing with the highest energy applied first at the moment of initial wetting (MOIW) followed by a "quiescent" zone allowing for more gentle activation as polymer science dictates.
- Extended residence time in the "quiescent" zone to optimize the continued charge site exposure as the polymer is activated in an optimal manner.
Our team of trained experts can help you determine the best technology for your application based on your process goals, the type of polymer used and the volume you are treating.
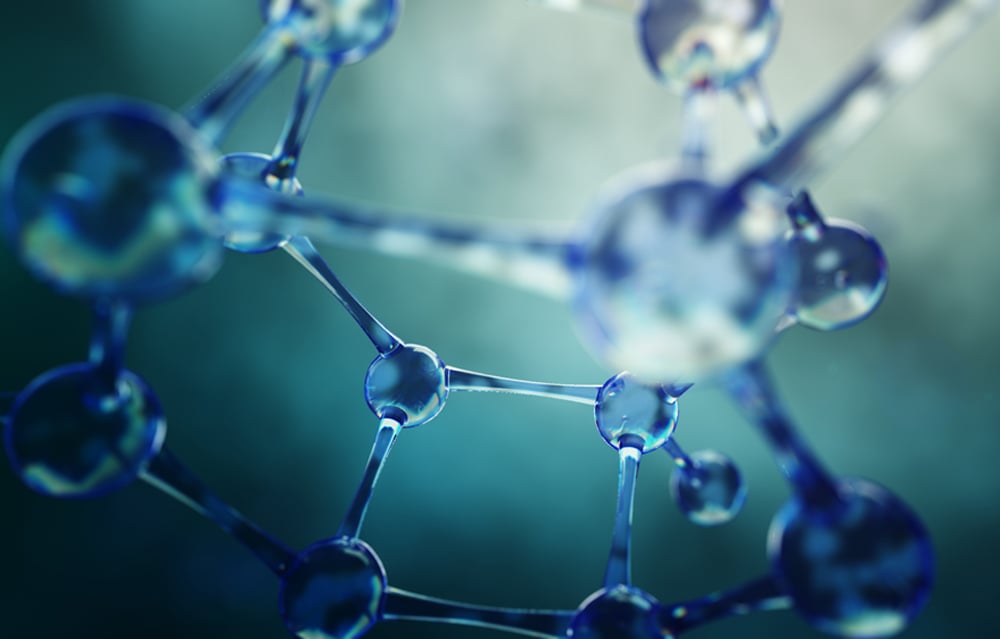
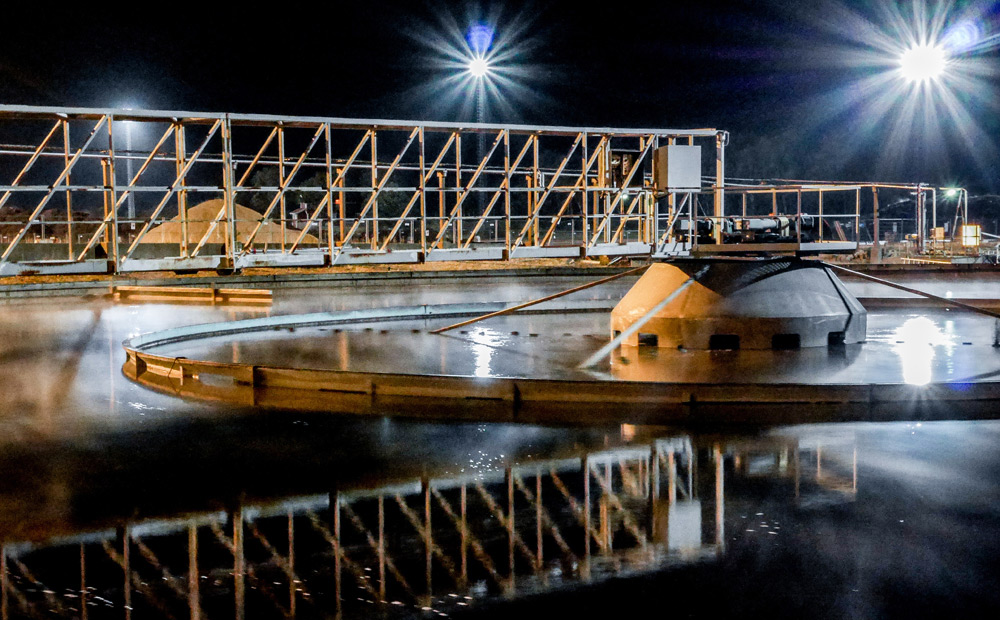
Optimize For Your Situation with Dry Polymer
The activation of the dry polymer can be achieved through a variety of means, including mechanical mixing, agitation, or the addition of other chemicals such as coagulants or flocculants.
The activation process is typically optimized for each specific application to ensure that the polymer is activated in the most effective way possible to achieve the desired results for your water or wastewater application.
Dry polymer has a shelf life of over 3 years if unopened and properly stored.
The Ideal Environment for Dry Polymer Activation
Dry polymer activation is a process used in wastewater treatment to enhance the flocculation and sedimentation of suspended solids in the wastewater. In dry polymer activation, the polymer is first mixed with a small amount of water to form a concentrated solution. The concentrated solution is then added to the wastewater and mixed thoroughly to ensure that it is evenly distributed throughout the wastewater. The polymer molecules then begin to interact with the suspended solids in the wastewater, causing them to coagulate and form larger flocs that are easier to remove from the wastewater.
To create the ideal environment for the first stage of dry polymer dissolution, crucial initial wetting occurs in the DD4 disperser. Here, polymer and water are subjected to high energy created by mechanical mixing. The dry polymer is accurately metered into the high-energy mix chamber and is properly activated with water. After brief exposure, the solution exits the high-energy disperser. The point of initial polymer / water contact is visible to the operator through a clear, acrylic interface.
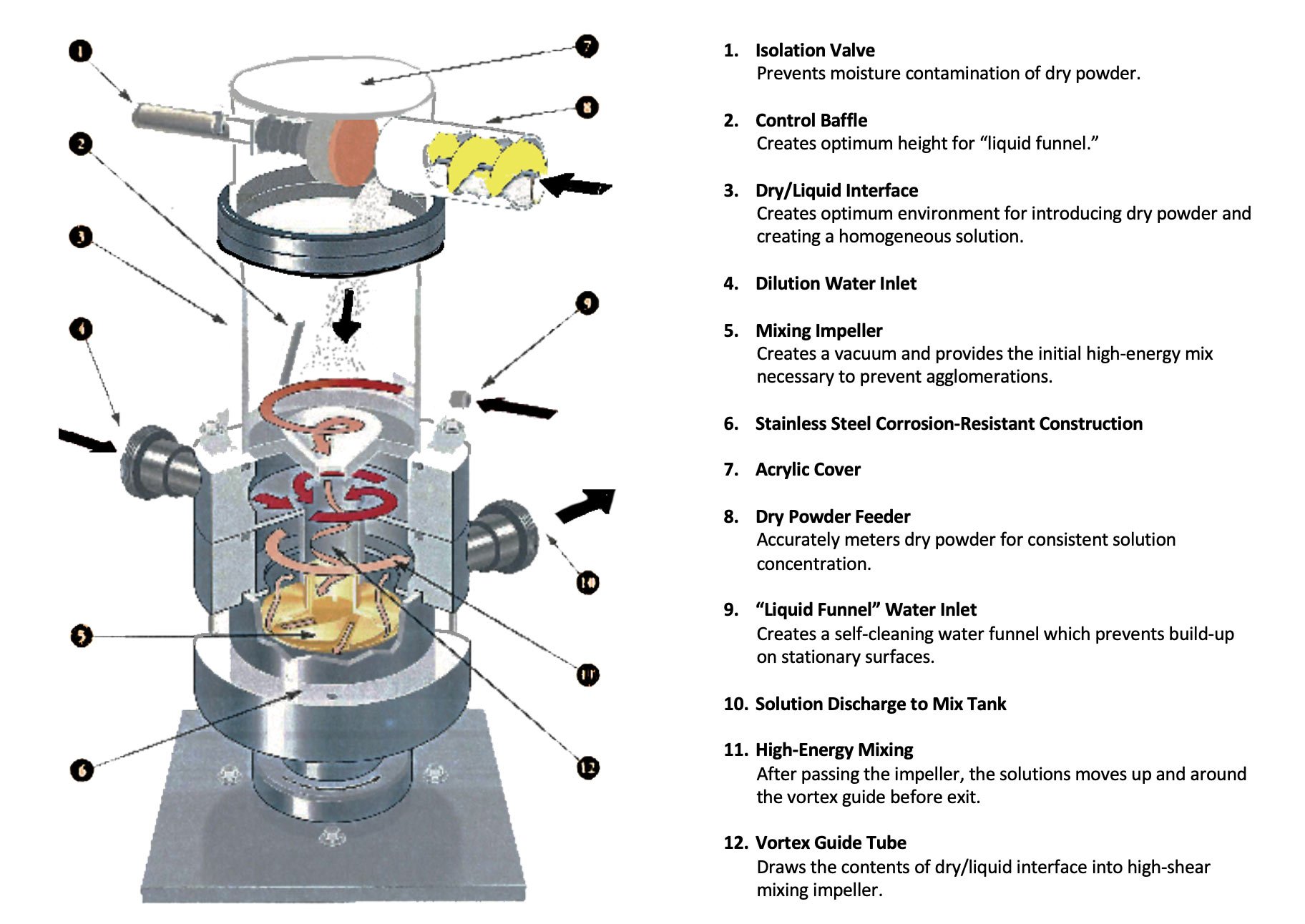
Creating the ideal environment for dry polymer activation.
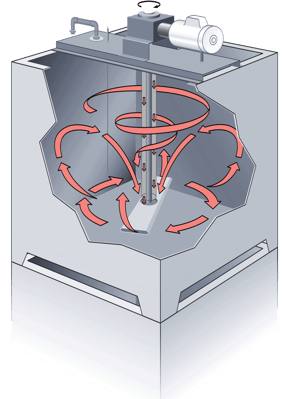
Low-Energy Mix Tanks Create Uniformity
Most polymer mix tanks are not uniform in their mixing energy. Agglomerations form in the portions of the tank that receive the least mixing energy, while polymer chains are broken up at the tip of the rotating mixing blade.
In contrast, the Polyblend® activated polymer storage tank is specifically designed to provide fully uniform mixing intensity. The rotating impeller, known as a “hollow wing,” has a length that is more than half the width of the tank. This unique design continuously moves the solution both vertically and horizontally, creating a pump-like action that reduces agglomerations and broken polymer chains. The square tank design eliminates the potential for a damaging vortex. With minimal waste, polymer costs are reduced and polymer activation performance is improved.
The hollow wing impeller design is available for use with various tank sizes up to 2,000 gallons. The hollow wing design is standard on all Polyblend® dry polymer systems and optional on Dynajet™ dry polymer systems.
Benefits of Dynajet™ Pneumatic Conveyance Systems
- Performs well with wide range of molecular weight polymers
- Low operating cost
- Low maintenance cost
- Multiple mixing chamber sizes
- Highly reliable
Polyblend®DP
Polyblend® DP systems have an unmatched reputation for reliability. The DP system typically reduces polymer consumption by 25% or more, while substantially improving polymer performance in terms of sludge dryness, solids capture, water clarity, drainage / retention, or any other measure.
DP110 Dry Polymer Feed System outperforms all other designs in head-to-head trials. While dry polymer feed systems are notoriously high maintenance items, the Polyblend® DP Series requires the least maintenance and operates unattended for a longer interval than any other dry polymer feed system on the market.
Available in a wide range of capacities up to 45 pounds/hour (20 kg/hour).
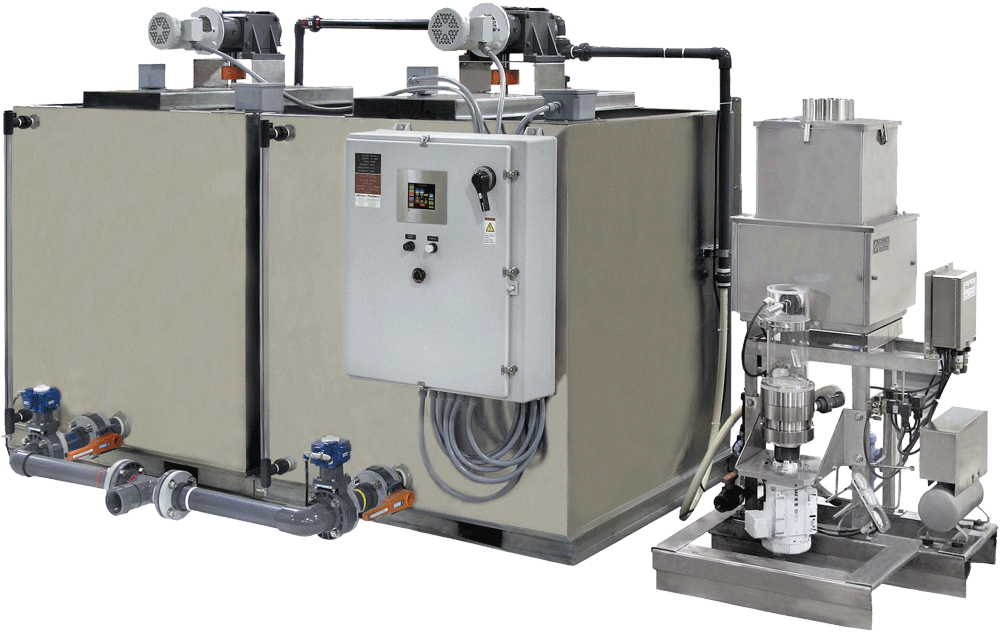
Features
- Reliable performance
- Field proven
- Reduced polymer consumption
- Fully automated operation
- Operator interface controls
- Improved safety features
- Easy to operate
Benefits
- An innovative stainless steel "Hollow Wing" Mixing Impeller reduces polymer consumption by providing proper energy at low speed through impeller size and recirculation to prevent agglomerations, while minimizing polymer fracture.
- Operation is fully automatic - the only thing the operator has to do is keep polymer in the hopper.
- The DP Series offers integral controls using the latest technologies.
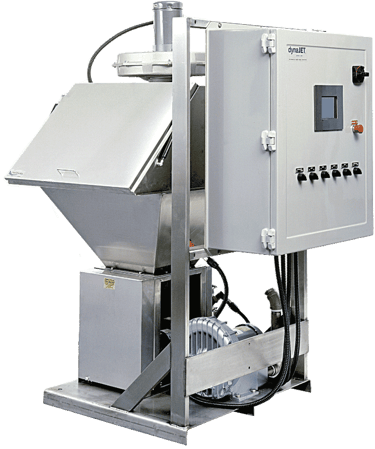
Dynajet™
The Dynajet™ technology uses a blower-induced pneumatic conveyance system to transfer up to 12 lbs of polymer per minute from the volumetric feeder to the wetting head, with higher capacity custom systems available.
The polymer is naturally dispersed in the conveyance air before introduction to the dilution water for optimum polymer-particle wetting. Polymer and water come together in a high flow shower of water produced by specially designed waterjets to ensure complete polymer-particle wetting.
The solution that’s created enters the mix tank where the polymer solution is ready for the mixing and aging process.
Features
- Shower type wetting process
- Pneumatic polymer conveyance system designed to disperse polymer prior to wetting
- NEMA 4x control panels
- Touch screen operator interface
- Hoppers designed for ease of polymer handling (available in multiple configurations)
- Stainless steel hopper
- Rugged stainless steel variable speed Volumetric feeder
- Stainless steel equipment skid
- Optional dust collector for manual fill hoppers
Benefits
- Assures thorough wetting of polymer for optimum performance, clean operation and increased reliability.
- Increased reliability and disperses polymer to assure effective polymer-particle wetting.
- Prevents polymer build-up at volumetric feeder, prevents plugging of polymer conveyance system.
- Choice of polymer storage and handling systems to meet your plants specific needs.
- Safer for the operator when loading polymer. Cleaner operation with less chance for polymer spills.
- Flexibility to choose the control features that best meet the needs of your plant without the increased cost of customization.
"The Polyblend® DP110 really allows us to be more efficient in polymer dosing and helps ensure environmental compliance – a win-win.”
Polyblend Mechanical Activation (Dry Polymer Feed Systems)
Overview of Polyblend® DP Series
*Numbers provided are @ 0.3% concentration. cleanwater1 does not recommend exceeding this concentration for a DP110 system.
Polyblend® DP110
The PolyBlend® DP110 is a lower cost option specifically designed to provide uniform mixing. Dry polymer and water are mixed in the vortex created by the rotating tank impeller. The unique mixing process provides maximum polymer preparation and activation.
Polyblend® DP500
The PolyBlend® DP500 consists of the DD4 dry polymer disperser, a fiberglass mix tank, and a gravity-fed fiberglass hold tank. The DP500 is specifically designed to provide uniform mixing. Dry polymer and water are initially mixed in the DD4 polymer disperser, exposing the solution to a high-shear agitation via mechanical mixing. The high-shear agitation ensures proper activation of the polymer and prevents unwanted agglomerations.
Polyblend® DP800
The PolyBlend® DP800 is an integrated equipment package capable of automatically preparing a homogeneous polymer solution. The DP800 consists of the DD4 dry polymer disperser, a stainless steel mix tank, and a gravity-fed stainless steel hold tank.
Polyblend® DP2000
The PolyBlend® DP2000 is an integrated equipment package capable of automatically preparing a homogeneous polymer solution. The DP2000 consists of the DD4 dry polymer dispenser and large side-by-side stainless steel mix and hold tanks.
Dynajet Hydraulic Activation (Dry Polymer Feed Systems)
Overview of Dynajet™ Series
Larger capacity systems available. Please consult your sales representative.
Dynajet™ Feature Diagram
Dynajet™ Tank-Top Frame Assembly
Which Technology is Right for You?
Our team of trained experts can help determine the best technology for your application. Because we are not limited to one technology, you can feel confident knowing we’re committed to finding the system that meets your process objectives.
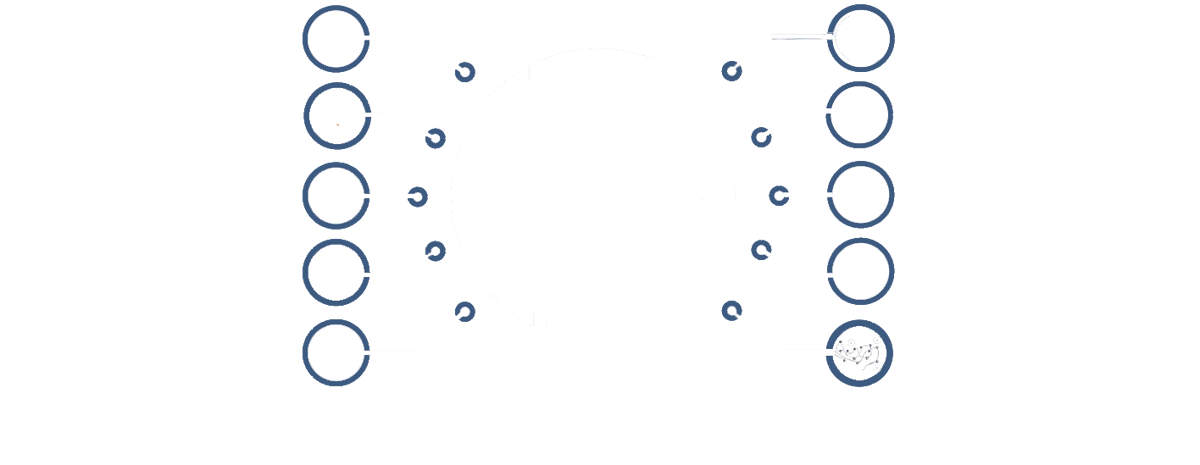
Featured Installations
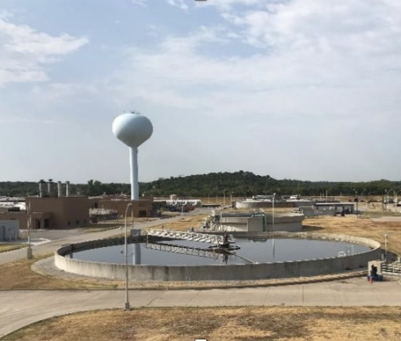
Forth Worth
Solution: Dynajet™ Dry Polymer System
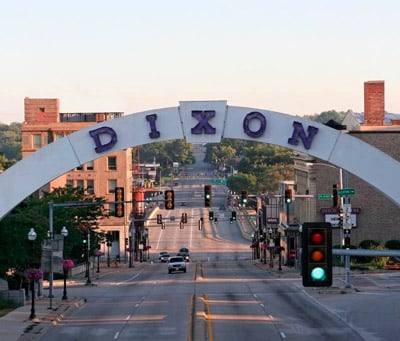
City of Dixon
Location: Dixon, Illinois
Solution: Polyblend® DP 800 Dry Polymer System
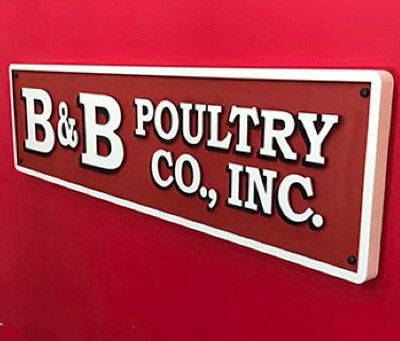
B&B Poultry Co., Inc.
Solution: Polyblend® Dry Polymer System
"PolyBlend® has been performing exceptionally well for Windsor, Ontario, for over two decades. With basic maintenance, we’ve needed very few parts over the years, and when you see the equipment, it is in excellent condition!"
Seeing Is Believing
Let us demonstrate the effectiveness of the PolyBlend® polymer mixing system with your existing or new application. We’re so sure you’ll be satisfied that we’ll bring the on-site trial to you for a side-by-side comparison at no charge.
Polymer Feed and Control Applications
- Drinking water
- Groundwater remediation
- Industrial process water
- Wastewater
- Water reuse and recycle
Experience It For Yourself
We’re so sure you’ll be satisfied with a demonstration on your existing or new application, that we’ll bring the on-site trial to you for a side-by-side comparison.
Available for Polyblend®, Dynablend™ and Dynajet™ polymer activation systems. Liquid PolyBlend® system demonstration units are also available.
- Ten emulsion systems operating in the field at any given time.
- Two trailer mounted dry polymer systems available.
- Highly successful program for customers and consulting engineers.
- Direct evidence of demonstrated polymer savings.
- Case studies available.
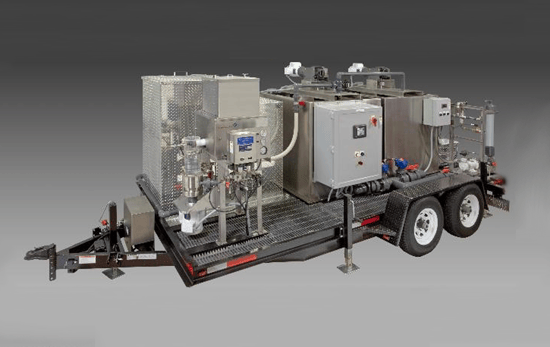
I just set the settings and walked away; it was extremely user-friendly. The way it blends and the resulting polymer solution – and the reduction in polymer usage – made this an excellent unit.”
Brad Anderson, O&M Tech V, Fairfield-Suisun Sewer District, CA
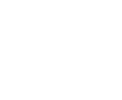
Let's get the conversation started
Tell us a little bit about you and the information you’re looking for and we'll send you information by email about the topics you are interested in. Check the box to have a cleanwater1 expert contact you within one business day.
Additional Resources
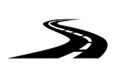
Learn At Your Pace
By subscribing to our learning track, you will receive emails featuring videos, webinar invites, informative articles and more.

View Our Online Library
Featuring brochures, case studies, data sheets and more. Filter by product category, brand, location, use case or document type.

Connect With Us
Contact a member of our team using our online form, by email or give us a call. We look forward to speaking with you.